The Essential Guide to LOLER Legislation in Home & Garden
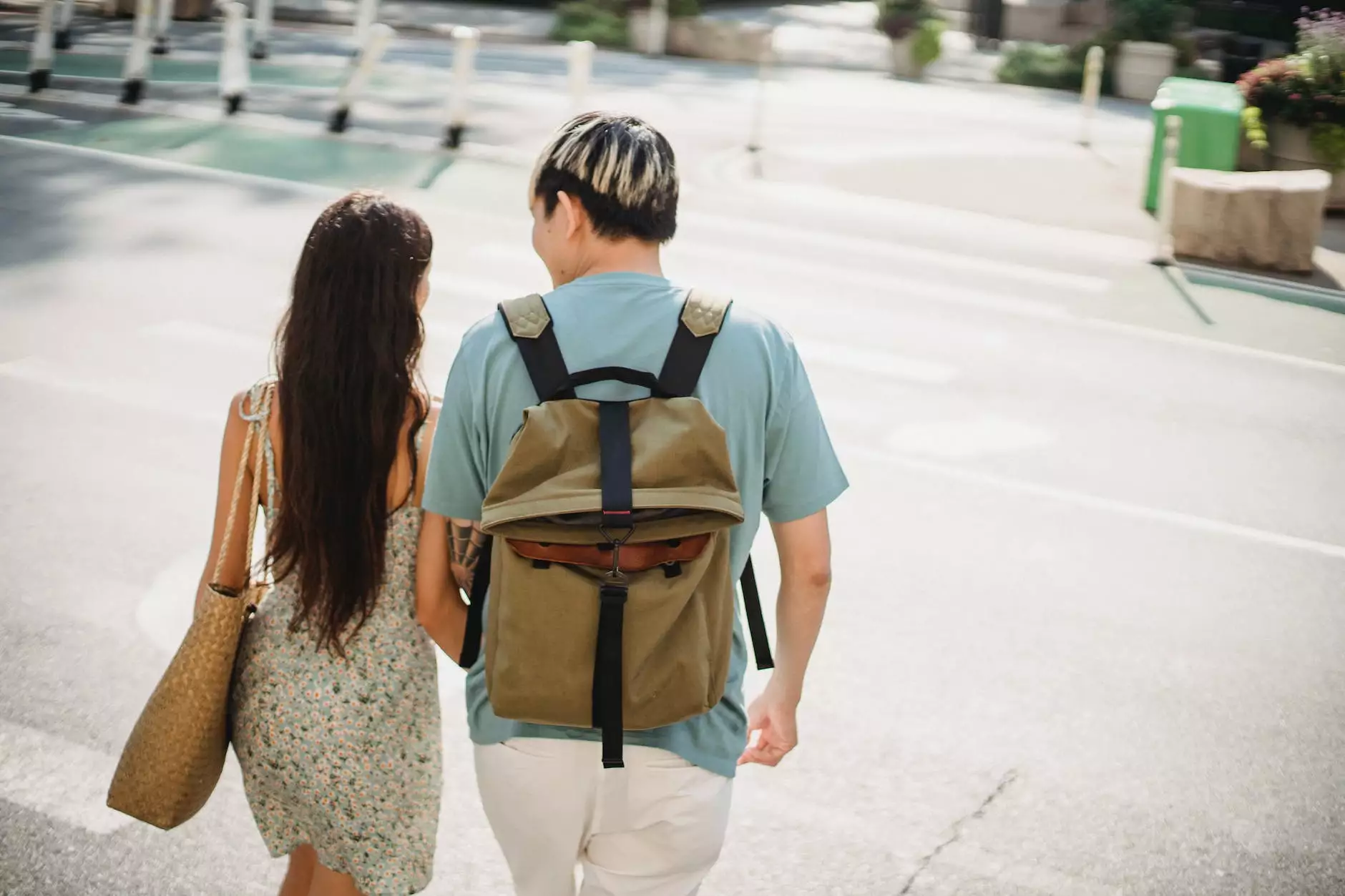
In today’s evolving regulatory environment, it’s crucial for both professional and amateur gardeners to understand the implications of LOLER legislation, especially within the context of safety in the home and garden sectors. In this article, we will delve deep into what LOLER legislation entails, how it affects gardeners and gardening businesses, and practical steps to ensure compliance.
What is LOLER Legislation?
The term LOLER stands for “Lifting Operations and Lifting Equipment Regulations.” Enacted in the United Kingdom, this legislation covers the use of lifting equipment in the workplace and aims to ensure that all lifting operations are performed safely. While it primarily focuses on industrial settings, its principles can also be applied to gardening and home improvement contexts, particularly involving lifting equipment such as hoists and lifts used in residential gardening projects.
Understanding these regulations is essential, especially for those who hire professionals or operate lifting gear in their gardening practices. Compliance not only promotes safety but also enhances the reputation of businesses in the gardening industry.
The Importance of Safety in Gardening
Gardening can involve several activities that pose risks, particularly when using machinery. The integration of LOLER legislation in gardening emphasizes the need for safety protocols that protect both individuals and the environment. Here are some key reasons why safety must be prioritized:
- Risk Reduction: Effective safety measures greatly reduce the risk of accidents.
- Legal Compliance: Adhering to LOLER helps avoid legal penalties and fosters a safe working environment.
- Enhancing Professional Reputation: A commitment to safety can significantly enhance your credibility and attract more clients.
- Protecting Equipment: Proper maintenance and operation of lifting equipment prolong its lifespan.
Who is Affected by LOLER Legislation?
LOLER applies to a broad range of individuals and organizations within the gardening sector, including:
- Professional Gardeners: Those who operate lifting equipment in their work must comply with LOLER.
- Homeowners Engaging Contractors: It’s vital to assess if contractors adhere to LOLER when hiring them for garden work involving heavy lifting.
- Pest Control Services: Businesses that use lifting equipment for pest control must ensure their practices are compliant.
- Garden Equipment Suppliers: Suppliers should guarantee that their equipment meets LOLER standards before renting or selling.
Key Requirements of LOLER Legislation
To comply with LOLER legislation, individuals and businesses must adhere to several key requirements:
1. Equipment Design and Manufacture
All lifting equipment must be designed and manufactured to specific standards that ensure its safety and reliability. This includes factors like:
- Robustness for prolonged use
- Clear instructions for safe usage
- Regular checks for manufacturing defects
2. Thorough Examination
LOLER mandates that lifting equipment undergoes a thorough examination before it is put into service and at regular intervals thereafter. This includes:
- Annual examinations for most lifting gear
- Detailed inspections by a competent person
- Documentation of examination results
3. Safe Usage and Operation
All users of lifting equipment must operate it safely. This means providing adequate training to staff, ensuring they understand:
- The risks involved in lifting operations
- How to properly operate the equipment
- Emergency procedures in the event of an accident
4. Maintenance
Ongoing maintenance is vital to ensure equipment remains safe to use. This includes:
- Regular servicing of machinery
- Keeping maintenance records
- Addressing any faults immediately
Best Practices for Compliance with LOLER Legislation
To ensure compliance with LOLER legislation, here are tried-and-tested best practices tailored for the gardening industry:
Training and Awareness
Providing training for staff on LOLER requirements is essential. Regular workshops and refreshers can enhance awareness and understanding of safety protocols.
Regular Equipment Audits
Conducting audits of lifting equipment can help identify any potential risks and ensure adherence to LOLER standards. This should include:
- Using a checklist for equipment checks
- Consulting with a qualified professional for inspections
Documentation and Record-Keeping
Maintaining comprehensive documentation regarding equipment inspections, training, and operational procedures is critical. This ensures that evidence of compliance is readily available, which can be crucial in the event of an incident.
Understanding the Implications of Non-Compliance
Failing to comply with LOLER can have serious implications, which include:
- Legal Consequences: Non-compliance can lead to significant legal repercussions, including fines or lawsuits.
- Increased Accident Rates: Attention to proper safety measures directly correlates to reduced accidents.
- Damage to Reputation: A business found non-compliant may face public backlash that can be detrimental to its brand.
Conclusion
Understanding and adhering to LOLER legislation is vital for ensuring safety in gardening operations, protecting workers and clients alike. By prioritizing safety measures, maintaining compliance, and fostering a culture of safety, businesses can not only meet legal requirements but also enhance their overall service quality.
As the gardening industry continues to evolve, staying informed about regulations like LOLER will empower gardeners and professionals to create safer, more efficient working environments. At Safe Plant UK, we advocate for the highest safety standards in the gardening sector, ensuring that every operation is conducive to the safety and well-being of all involved.