Understanding Injection Molded Plastic: A Business Perspective
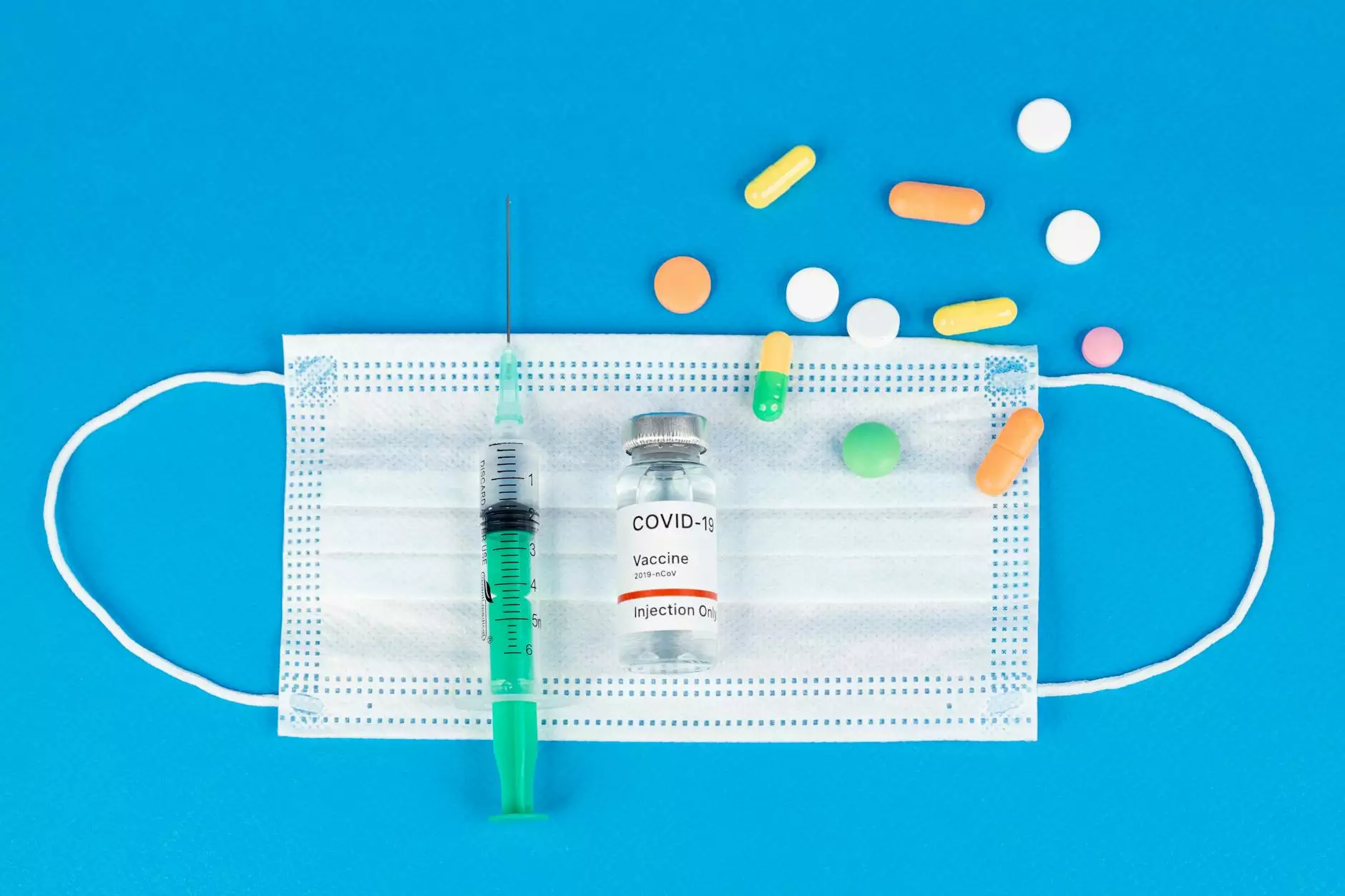
The Significance of Injection Molded Plastic in Modern Business
In today’s competitive manufacturing environment, injection molded plastic has emerged as a crucial component, significantly influencing the outcome of various industries, particularly within metal fabrication. Businesses that leverage advanced techniques in plastic injection molding can streamline their production processes, enhance product quality, and drive profitability. This article explores the advantages, applications, and best practices surrounding injection molded plastic in the context of modern business.
What is Injection Molded Plastic?
Injection molded plastic is a manufacturing process where molten plastic is injected into a mold to create parts or products. This process allows for highly intricate designs and can accommodate a myriad of materials, enabling the production of both small and large items with great precision.
The Process of Injection Molding
The injection molding process consists of several stages, including:
- Clamping: The two halves of the mold are closed and securely clamped together.
- Injection: Molten plastic is injected into the mold under pressure.
- Cooling: The plastic is allowed to cool and solidify, taking the shape of the mold.
- Opening: The mold is opened, and the finished product is ejected.
- Finishing: Any necessary finishing processes, such as trimming or surface treatment, are conducted.
Key Benefits of Using Injection Molded Plastic
Incorporating injection molded plastic into production lines offers numerous benefits for businesses, including:
- Cost-Effectiveness: Injection molding techniques significantly reduce production costs in high-volume manufacturing.
- Design Versatility: The ability to create complex geometries and designs with high precision allows for innovation in product development.
- Increased Efficiency: The speed of the injection molding process enables companies to produce large quantities of products in shorter time frames.
- Lower Material Waste: Compared to other manufacturing methodologies, injection molding produces minimal waste, thus supporting sustainability initiatives.
- Superior Quality: The capability to maintain tight tolerances and uniformity ensures that the final product meets high-quality standards.
Applications of Injection Molded Plastic in Metal Fabrication
The intersection of injection molded plastic and metal fabrication is a fascinating area, offering innovative solutions across multiple sectors. Here are some notable applications:
Automotive Industry
In the automotive sector, businesses utilize injection molded plastic for manufacturing components such as dashboards, bumpers, and other interior parts. The integration of these parts reduces the overall weight of the vehicle, contributing to improved fuel efficiency.
Aerospace
The aerospace industry benefits from injection molded plastic in creating lightweight components, which are critical for enhancing aircraft performance and reducing operational costs. Plastic parts also offer resistance to corrosion and other environmental factors.
Consumer Products
Household items, consumer electronics, and packaging solutions frequently employ injection molded plastic. Its adaptability allows manufacturers to innovate and cater to the evolving preferences of consumers, providing aesthetically pleasing and functional designs.
The Role of Injection Molded Plastic in Sustainability
As global awareness of sustainability increases, businesses are searching for ways to enhance their ecological footprints. Injection molding can play a significant role in these initiatives:
- Recyclability: Many types of injection molded plastics are recyclable, allowing manufacturers to minimize waste.
- Energy Efficiency: The rapid production cycle of injection molding often consumes less energy compared to alternative manufacturing methods.
- Material Conservation: With low material waste generated during the molding process, companies can optimize their resource use.
Challenges in the Injection Molding Process
While the benefits of using injection molded plastic are abundant, several challenges can face manufacturers:
- High Initial Costs: Setting up injection molding production lines can involve significant capital expenditures, making it less accessible for smaller businesses.
- Mold Design Complexity: Creating and maintaining molds that can produce high-quality parts requires expertise and can be time-consuming.
- Material Limitations: Not all plastics are suitable for injection molding, and the choice of material can impact the final product's properties.
Best Practices for Successful Injection Molding
To maximize the benefits of injection molded plastic, businesses should adhere to several best practices:
- Invest in Quality Molds: Working with experienced experts to develop high-quality molds can significantly improve production outcomes.
- Select the Right Material: Engage in thorough research to choose the appropriate plastic material based on the application and performance requirements.
- Optimize the Process: Continuous monitoring and adjustment of the injection molding parameters can lead to enhanced efficiency and product quality.
- Embrace Technology: Leverage CAD software and simulation tools to predict and enhance mold performance before production.
- Sustainability Focus: Incorporate recycling and waste management strategies to enhance corporate social responsibility and attract environmentally conscious consumers.
The Future of Injection Molded Plastic in Business
The ongoing advancements in technology will shape the future of injection molded plastic, presenting new opportunities for businesses. Innovations in materials, such as biodegradable plastics and composites, promise to enhance the sustainability of products. Additionally, as automation and smart manufacturing techniques evolve, companies can expect further reductions in costs and improvements in efficiency.
Conclusion
In summary, injection molded plastic stands as a cornerstone of modern manufacturing, particularly for businesses involved in metal fabrication. The numerous benefits it offers, coupled with its versatile applications, ensure that companies can enhance their operational efficiency while contributing to sustainability. As the landscape of manufacturing continues to evolve, staying informed about the latest trends in injection molding will enable businesses to maintain a competitive edge. For more insights and innovative solutions in metal fabrication and injection molded plastic, consider visiting deepmould.net.